
Inside
Swan
Many elements in
the making of a Swan have earned Nautor's Swan their enviable reputation
as the world's premier production yacht builder, setting the standards
for quality, performance and safety by which others are judged. Some
of these only become apparent upon closer inspection of each yacht,
with the attention given to detail, both above and below the deck.
The joinery operation,
starts with teak planks arriving at the factory still strapped in the
original shape of the trunk.
Being
conscious of the world's dwindling supply of teak, Nautor's Swan buys
only from those plantations that plant one tree for every one felled.
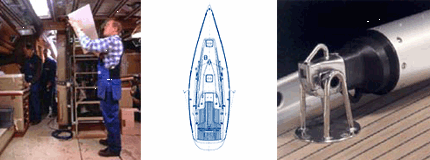
Once at the factory,
the teak is sliced into veneer flitches. These are then carefully selected
for colour and grain, before being glue-stitched together and bonded
to the plywood used in the bulkheads and interior cabinetry.
The
wooden templates once used to define the shapes of bulkheads and other
parts are gradually being replaced by digital system driving computer-controlled
cutting machinery.
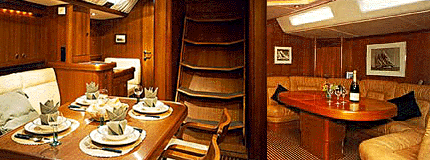
Wood laminations
are fashioned under heat and pressure to produce the soft, flowing curves
of fiddles, door mouldings and other joinery parts. Pre-glued veneers
are draped into one of approximately 100 specially constructed templates
within a 160 ton capacity press, to compact then into their final shape.
A ten-minute burst of microwave energy follows to cure the glue.
In other bays of
the joinery shop, craftsmen work to fashion and assemble the interior
components, giving the famous Swan interior satin sheen to the wood.
Samples of the various
joinery parts with their own unique grain are even kept in storage to
ensure a perfect match, should any refit or replacement joinery work
be required in the future.
The
yard
The history
The tradition of innovation
Inside swan
A talent for design
|